Energy Harvesting Sensor for preventive maintenance of Bearings
Bearings are a critical component in rotating machinery. Bearing failure leads to machine breakdown. Monitoring of bearing is required for the reliable functioning of the machine and reduction of its maintenance cost. Harsh operating conditions lead to bearing failure indicators like increased vibration, rise in temperature and corrosion.
The goal of this project was to non-invasively sense rise in bearing temperature for pre-emptive maintenance. A novel idea using Neodymium magnets was explored for this purpose and a wireless sensor node running off harvested energy was developed which would potentially reduce the need for human interference.
Neodymium magnets are highly sensitive to changes in temperature. The change in their magnetic field can be used as an indirect measure of change in temperature. Also, since the magnets are placed on the rotating bearing element, a rotating magnetic field is produced which can be taken advantage of by placing a small coil at a distance(similar to an axial flux generator). The small amount of energy harvested from this arrangement was enough to power the prototype sensor.
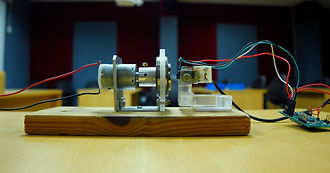
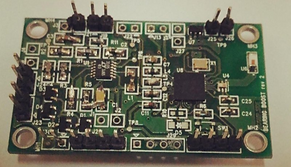
Prototype setup consisting of a motor test-beed, ball bearing, Neodymium magnet arcs and sensor PCB
5cm x 4cm 2-layer board incorporating power conditioning, microcontroller and BLE communication functional blocks
5cm x 4cm 2-layer board incorporating power conditioning, microcontroller and BLE communication functional blocks